Fasteners and Machining: Customized Solutions for each Manufacturing Requirement
Browsing the World of Fasteners and Machining: Strategies for Precision and Rate
In the complex world of bolts and machining, the pursuit for accuracy and rate is a continuous challenge that demands careful focus to information and calculated preparation. From recognizing the varied selection of bolt kinds to choosing optimum products that can hold up against strenuous needs, each action in the procedure plays a crucial duty in accomplishing the wanted end result.
Understanding Bolt Kind
When picking fasteners for a job, understanding the different kinds available is crucial for guaranteeing ideal performance and integrity. Bolts are made use of with nuts to hold products together, while screws are flexible fasteners that can be made use of with or without a nut, depending on the application. Washers are essential for dispersing the lots of the fastener and avoiding damages to the material being fastened.
Choosing the Right Products
Understanding the significance of picking the right materials is extremely important in guaranteeing the ideal efficiency and integrity of the chosen fastener types reviewed formerly. When it pertains to bolts and machining applications, the product selection plays a crucial role in figuring out the total strength, toughness, corrosion resistance, and compatibility with the designated atmosphere. Various products offer varying residential or commercial properties that can substantially influence the efficiency of the bolts.
Usual materials made use of for fasteners consist of steel, stainless steel, aluminum, brass, and titanium, each having its unique strengths and weaknesses. Steel is renowned for its high toughness and sturdiness, making it appropriate for a vast array of applications. Stainless-steel uses exceptional rust resistance, suitable for environments prone to moisture and chemicals. Light weight aluminum is corrosion-resistant and light-weight, making it ideal for applications where weight decrease is crucial. Brass is often picked for its visual charm and exceptional conductivity. Titanium is recognized for its exceptional strength-to-weight ratio, making it ideal for high-performance applications. Picking the appropriate material involves considering variables such as stamina requirements, environmental conditions, and spending plan restrictions to guarantee the desired performance and longevity of the bolts.
Precision Machining Techniques

Along with CNC machining, various other precision techniques like grinding, turning, milling, and exploration play vital roles in bolt production. Grinding helps attain fine surface look here area coatings and tight dimensional tolerances, while transforming is commonly used to produce round components with accurate sizes. Milling and boring procedures are essential for shaping and developing holes in bolts, ensuring they satisfy specific specifications and function appropriately.
Enhancing Rate and Efficiency
To maximize fastener production procedures, it is vital to streamline find out here operations and implement efficient approaches that complement precision machining methods. One crucial approach for enhancing speed and effectiveness is the application of lean production concepts. By minimizing waste and concentrating on continual improvement, lean practices assist maximize and remove traffic jams workflow. In addition, buying automation modern technologies can substantially enhance manufacturing rate. Automated systems can take care of recurring tasks with precision and speed, enabling workers to concentrate on more complex and value-added activities. Adopting Just-In-Time (JIT) inventory monitoring can likewise improve efficiency by making sure that the appropriate materials are readily available at the correct time, minimizing excess supply and lowering preparations. In addition, cultivating a culture of cooperation and interaction among group participants can improve total effectiveness by promoting transparency, analytic, and development. By incorporating these strategies, suppliers can accomplish a balance in between speed and accuracy, eventually improving their affordable side in read review the fastener market.
Quality Control Procedures
Implementing rigorous quality assurance actions is vital in making certain the dependability and consistency of bolt products in the manufacturing procedure. Quality control procedures include numerous phases, beginning with the selection of basic materials to the last examination of the ended up bolts. One essential facet of quality control is carrying out thorough material examinations to confirm compliance with requirements. This entails assessing variables such as material structure, sturdiness, and strength to assure that the bolts fulfill sector criteria. In addition, keeping track of the machining processes is important to promote dimensional precision and surface area coating high quality. Using advanced innovation, such as computerized inspection systems and accuracy measuring devices, can boost the precision and effectiveness of quality assurance procedures.
Routine calibration of tools and equipment is crucial to preserve consistency in manufacturing and guarantee that bolts meet the necessary tolerances. Applying strict procedures for determining and attending to flaws or non-conformities is important in protecting against substandard items from getting in the marketplace. By establishing a thorough quality control framework, suppliers can copyright the credibility of their brand and supply bolts that meet the greatest criteria of efficiency and sturdiness.
Final Thought
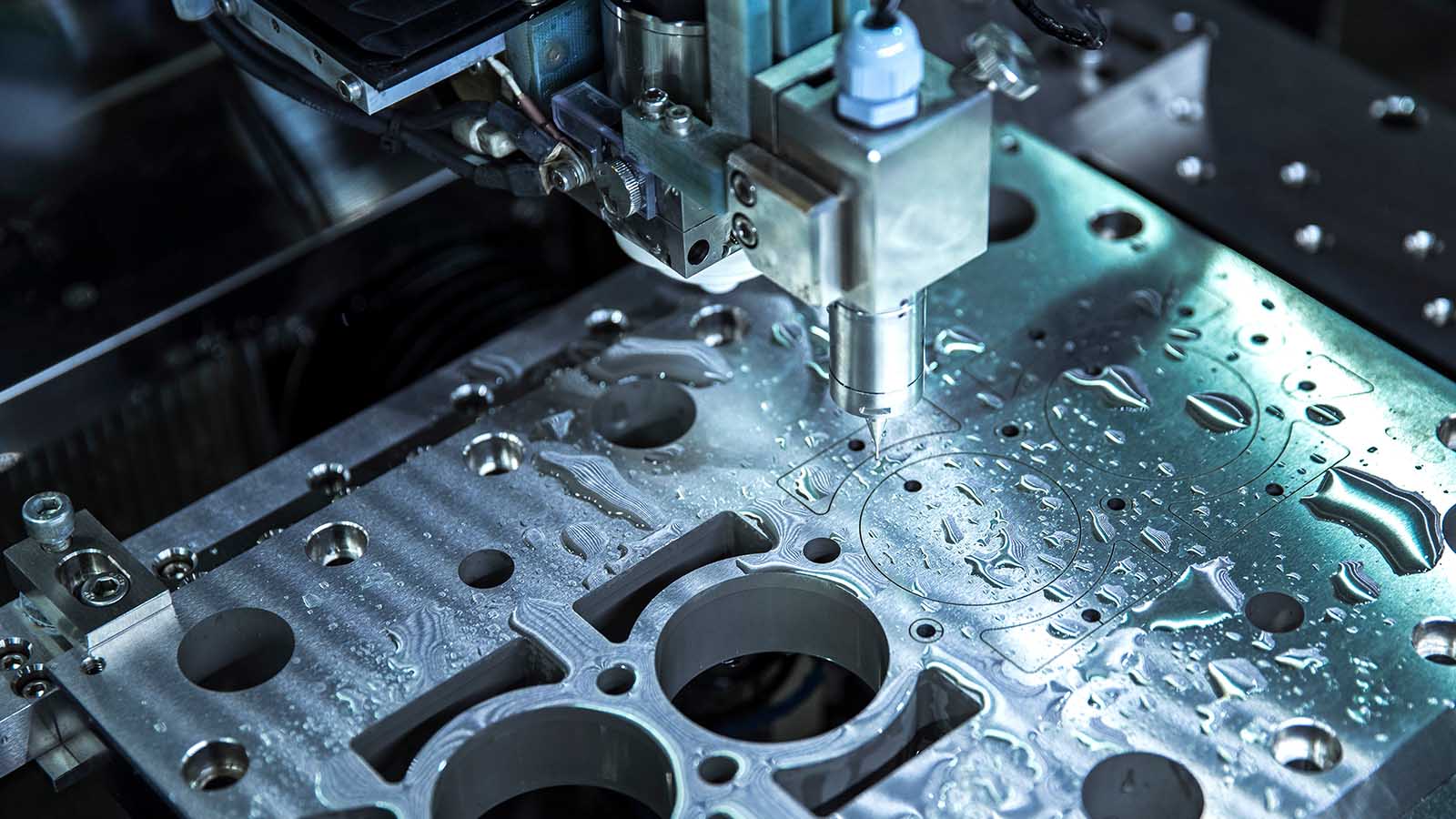
In the elaborate world of fasteners and machining, the mission for accuracy and rate is a continuous obstacle that requires thorough focus to detail and calculated planning. When it comes to bolts and machining applications, the product option plays an important function in establishing the total toughness, longevity, rust resistance, and compatibility with the designated atmosphere. Precision machining includes various innovative methods that ensure the limited tolerances and specifications required for fasteners.In enhancement to CNC machining, other accuracy strategies like grinding, transforming, milling, and boring play important roles in bolt production.To maximize fastener manufacturing processes, it is essential to streamline procedures and carry out efficient strategies that enhance accuracy machining strategies.